Getting Started: Basic Workshop Setup
A proper bladesmithing workshop requires careful planning for safety, organization, and basic tooling. Essential safety equipment protects against sparks, dust, and heat, while systematic organization ensures efficiency. Beginning bladesmiths should focus on acquiring fundamental hand tools before investing in expensive power equipment.
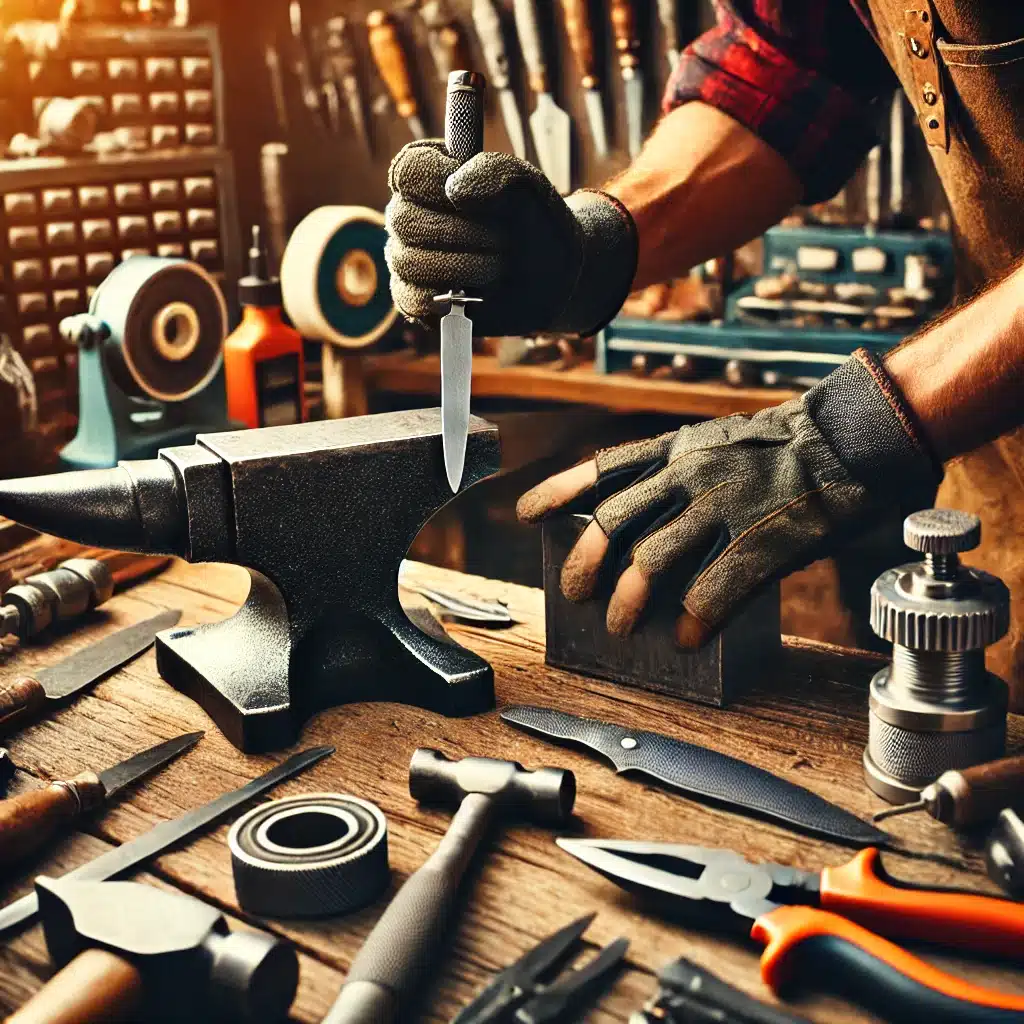
Essential Safety Equipment
Building a proper workshop starts with the right safety equipment and organization systems. Our curated selection at National Site Supplies ensures your workspace meets professional standards from day one.
Safety gear forms the foundation of responsible bladesmithing. A proper setup includes ANSI Z87+ rated safety glasses, heat-resistant gloves rated for 2000°F, and a NIOSH-approved respirator with P100 filters. Secondary protection includes leather aprons, sleeve protectors, and steel-toed boots to guard against falling objects and hot metal.
Workshop safety extends beyond personal protection. Install multiple ABC-rated fire extinguishers within easy reach, maintain a first aid station, and ensure proper electrical safety with GFCI outlets. Regular safety equipment inspections and replacements prevent equipment degradation from heat and chemical exposure.
Workspace Organization
Efficient workspace layout separates hot work, grinding, and assembly areas. Create dedicated zones for each major process: forging area with anvil and forge, grinding area with dust collection, and clean assembly space for final work. Store frequently used tools within arm’s reach of their use location.
Tool organization systems should prioritize both accessibility and protection. Use magnetic tool strips, pegboards, and rolling tool chests. Implement a shadow board system where tool outlines are drawn on the board, making missing tools immediately apparent. This organization system reduces time spent searching for tools and prevents damage.
Basic Hand Tools for Beginners
Essential hand tools for novice bladesmiths:
Category | Essential Tools |
---|---|
Layout | Scribe, squares, calipers |
Removal | Files, rasps, sandpaper |
Shaping | Hammers, tongs, punches |
Assembly | Clamps, screwdrivers, pliers |
Start with high-quality versions of these basic tools before expanding. Each tool should serve multiple purposes to maximize value. Quality files and hammers, in particular, will remain useful even as your workshop grows to include power tools.
Blade Shaping and Grinding Equipment
The blade shaping process requires both powered and manual tools for stock removal and refinement. Modern bladesmiths typically center their operations around a quality belt grinder, supplemented by hand tools for detail work and specialized equipment for surface finishing.
Belt Grinders and Accessories
A 2×72-inch belt grinder serves as the primary shaping tool in most shops. Key features include variable speed control (2000-4000 SFPM), quick belt change capability, and multiple work rests. Essential accessories include flat platens, contact wheels of various diameters, and a selection of belts ranging from 36 to 600 grit.
Belt selection and maintenance significantly impact grinding efficiency:
- Ceramic belts: Stock removal (36-120 grit)
- Aluminum oxide: General purpose (120-400 grit)
- Silicon carbide: Finishing (400+ grit)
- Trizact: Final finishing and polish
Hand Filing Tools
Strategic hand filing requires proper technique and appropriate tools. Essential files include a 12-inch bastard cut flat file, half-round file, and needle files for detail work. File selection should match the material—use Swiss-pattern files for hardened steel and traditional files for softer materials.
File maintenance affects both performance and longevity. Clean files regularly with a file card, store them separately to prevent edge damage, and replace when dull. Proper technique involves using the full length of the file with even pressure, lifting on the return stroke to prevent dulling.
Surface Finishing Equipment
Surface finishing requires progression through increasingly fine abrasives. A quality buffer/polisher with both cloth and felt wheels handles final polishing. Standard progression: 120-grit belt finish → 400-grit hand sanding → buffing with black compound → final polish with white compound.
Maintaining consistent angles and even pressure during finishing requires proper technique and appropriate tools. Use backing plates for flat surfaces and radiused accessories for curved areas. Proper speed control prevents overheating, which can damage both the blade and finishing accessories.
Heat Treatment Setup
Proper heat treatment requires precise temperature control, appropriate quenching media, and safety measures. A quality forge or kiln forms the foundation, supported by accurate temperature monitoring and properly configured quenching stations for consistent hardening results.
Forge Types and Selection
Gas forges offer precise temperature control and clean heating environments. Two-burner forges with internal dimensions of at least 4″x4″x12″ accommodate most knife blanks. Consider insulation quality, burner design, and door configuration when selecting a forge. Ribbon burners provide more even heating than jet burners.
Electric kilns offer excellent temperature consistency but slower heating cycles. Key features include digital controllers, multiple heating elements, and proper ventilation. Program capability allows for complex heat treatment cycles, particularly useful for stainless steels and specialized alloys.
Temperature Control Equipment
Accurate temperature measurement combines multiple tools:
Tool Type | Use Case | Accuracy Range |
---|---|---|
Pyrometer | General monitoring | ±25°F |
IR Thermometer | Surface temps | ±15°F |
Temperature crayons | Critical points | ±25°F |
Thermocouples | Digital control | ±5°F |
Calibrate temperature measurement tools regularly against known standards. Cross-reference between different measurement methods to ensure accuracy during critical operations.
Quenching Stations
Dedicated quenching stations should include:
- Primary quench tank (10+ gallons)
- Secondary temper bath
- Agitation system
- Temperature monitoring
Maintain separate tanks for different quenchants (oil, water, brine). Use containment systems to prevent spills and incorporate proper ventilation for oil quenching.
Specialized Tools for Advanced Techniques
Advanced bladesmithing techniques require specialized tools for pattern welding, chemical etching, and custom fixture creation. These tools expand creative possibilities while ensuring consistent results across complex processes.
Pattern-Welding Equipment
Pattern welding requires:
- Hydraulic press (minimum 20-ton)
- Clean flux application tools
- Specialized tongs
- Surface preparation equipment
Maintain separate tools for pattern welding to prevent contamination. Use high-temperature flux and appropriate welding temperatures for different steel combinations.
Etching Supplies
Essential etching supplies include:
- Acid-resistant containers
- Neutralizing solutions
- Temperature control system
- Proper ventilation setup
Follow strict safety protocols for acid handling and storage. Maintain separate workspaces for etching operations and store chemicals appropriately.
Custom Jig Making Tools
Develop custom jigs using:
- Metal stock (aluminum, steel)
- Precision measurement tools
- Tapping and threading equipment
- Fixture clamps
Document successful jig designs for repeatability. Test jigs thoroughly before using them on final products.
Workshop Safety Systems
Proper safety systems protect against fire, respiratory hazards, and physical injury. Comprehensive ventilation removes harmful particulates and fumes, while fire prevention systems and personal protection create multiple safety layers.
Ventilation Equipment
Install dust collection systems with minimum 1000 CFM capacity and 1-micron filtration. Main components include collection hoods at grinding stations, ductwork sized for proper air velocity, and filtered exhaust systems. Secondary ventilation addresses forge gases and chemical fumes through dedicated exhaust fans.
Cross-ventilation helps maintain workshop air quality. Position intake and exhaust points to create directional airflow away from work areas. Regular system maintenance includes filter changes, duct cleaning, and performance testing.
Fire Safety Setup
Fire prevention systems require:
- Class ABC extinguishers every 30 feet
- Smoke/heat detectors
- Emergency shutoffs for gas/electrical
- Fireproof storage for flammables
Maintain clear access to all safety equipment and exits. Regular testing and inspection schedules ensure system reliability when needed.
Personal Protection Gear
Essential PPE includes:
Type | Specifications | Use Case |
---|---|---|
Eye Protection | ANSI Z87+ | All operations |
Respirator | P100/OV | Grinding/chemicals |
Gloves | Heat/cut resistant | Material handling |
Hearing | 25+ NRR | Power tools |
Keep spare PPE readily available for visitors and replacement needs. Establish clear PPE requirements for different workshop areas and operations.
Quality Control and Measurement Tools
Precision measurement ensures consistent quality across all knife-making stages. Regular calibration and proper tool usage maintain accuracy in critical dimensions and performance characteristics.
Precision Measuring Instruments
Essential measurement tools:
- Digital calipers (0.001″ accuracy)
- Angle gauges (±0.5° accuracy)
- Thickness gauges
- Surface plates
Maintain calibration records and regular accuracy checks. Store precision tools in protected environments away from dust and vibration.
Hardness Testing Equipment
Rockwell hardness testing requires:
- Calibrated tester
- Test blocks
- Surface preparation tools
- Documentation system
Follow standardized testing procedures and maintain detailed records of results for quality control tracking.
Edge Geometry Tools
Edge testing equipment includes:
- Microscopes (10-60x)
- Edge angle guides
- Cutting performance tests
- Documentation tools
Standardize testing procedures and maintain reference samples for consistency in edge geometry evaluation.